As I mentioned in The 0 Euro Tuning post there are some vibrations and I wanted to see if I could get rid of them.

I found a silicon o-ring what fit just perfect over the rod.

then I rearanged the rollers to see if that would have any effect.

Well Murpy went with me to the test ride.
With the 4 rollers setup this way the engine run higher rpm much more early. Before I reached 100 km/h I was already over 7500 rmp full throttle. So it is not only the weights, but also the way they are placed in the pulley - fascinating.
After some hight rpm on the motorway I suddenly heard a high screeching noise. Luckily I was just out of a tunnel and there was an emergency lane. I stopped instantly and saw that I nearly had lost my
My wife had to play road service and bring me my tools.

Luckily the 27 mm nut could be tightened on the road via simulating the torque wrench.
I gave several sharp smacks with my hand on the rod, then run the engine for 2 seconds so the belt could slip up into the pulley and repeated this 3 times.
The ride home was not above 5000 rpm and I checked twice to see it the nut was still tight and she was. Good nut, have a cookie.
At home I took the transmission again apart and saw that my silicone ring had disintegrated.
To check if the vibrations had to do with the 4 roller setup I installed 6 rollers.
I had the 4 rollers in for 2 months and 2000 km and it did not bug me a bit but after I had the 8 rollers back in for a test something happened and I noticed the vibrations more with the 4 roller setup.
So here now for all of you who wonder how a CVT looks from the inside and for all of you who wonder where that left over washer has to go here now a step by step reassembly.

this is how the parts sit inside the metal lid

you see why the clutch gets hot, the hot air exhaust opening is above the clutch area.

Left the driving pulley with the roller wights, right the driven pulley what sits on top of the clutch.


When the rpm increase the gap between the clutch and the pulley gets smaller and cuts of most of the clutches air circulation.

When the centrifugal force is big enough the rollers are forced outside and slide up a ramp inside their pulley cage and they press against the plate and the pulley. This moves the both pulley halves together and the belt rides up in the pulley. This forces the driven pulley to separate more and the belt slides down in the driven pulley. This increases the rpm of the rear wheel.

The naked case with the rod from the engine on the left, the anti belt flapper wheel in the middle and the rod from the rear wheel gear box to the right

driving pulley half with the plate extreme extended (more than it extends while working)

the unit from above installed. When you take it out and you do not grab behind it to pull it out, the rollers and plastic guides fall out easily.

The case is so tight, that the belt leaves some marks on it.

Since I had not the right tools to on the road to take the transmission apart to squeeze the belt into the driven pulley I tried out if the whole thing could be reassembled without the squeezing from the driven pulley via brute force.
So I just pressed it on the ground so that the pulley would separate a bit to allow the belt to slide in to be flush with the pulley. Otherwise it will not fit in the case.

So I did not miss use my trusty bolt cutter for squeezing this time.

You need to hold the belt together for sliding the pulley in.

The spacer washer comes in now (see thumb). His job is to let the belt slide in a bit more to give you some extra rpm at low speed.

Now the other half of the pulley slides on. These air fins are creating the air blow.
2 thick washers go on top of it.

since we have not squeezed the driven pulley apart we need to to squeeze the belt a bit together (see above) so that there is nearly no interference with the both pulley halves.

The belt between the pulley halves with the nut tightened.

I needed to rotate the driving pulley 2 times to get the belt free and re tighten the nut again with the torque wrench. Test ride confirmed that this works well too, and this time I had the 27 mm wrench with me (picture #4 from above) to be safe.

Now the clutch bell slips on and the small washer follows. His job is to press against the center ball bearing ring.

The metal lid with the abrasions (left) from when the nut came loose and the air fins scraped on it.
On the right you see the ball bearing which stuck so badly on the rod that I had to buy a professional puller to separate them.

The small washer goes on first to sit on the ball bearing ring and then the big washer on top followed by the 21 mm nut.

Everything is back together just need to tighten the four 10 mm bolts and the seven 8 mm bolts.

These are all the tools you need to do this job, plus a Phillips head screw driver to the the silver plastic cover off (4 screws).
Thankfully the Malaguty engineers did not design any tupperware around the transmission.
In case of the Spidermax you just need to remove 2 hex screws to get the pillion foot rest out of the way.
And that´s it.
Just wanted to see what rollers are made off. I think it is a shame to throw them away just because the plastic surface has some abrasions. They could make them, so the metal part could be reused.

My next project will be to see if I can make some do it yourself rollers.
It is not because I do not want to buy a new set, but to see if I can change the characteristic to an even more optimal setting and it is just too much fun to tinker around and see what the engineers miss.
Update 2009.09.15
Back to 8 rollers 4 with a wooden center 4 normal with steel insert. More about that in the next post. The vibrations are still there, so it is not the amount of rollers I put in but something else. I suspect now the ball bearing from the driven pulley. When I turn it by hand (finger in the center hole) there is a noticeable clacking sound and feeling that something is not a happy round ball in there. So will get a new one, 40 mm outside 17 mm hole and 12 mm wide. I think it got bad when I tried to get the metal case of the transmission and had to use force.
Update 2009.9.18
Changed the ball bearing today
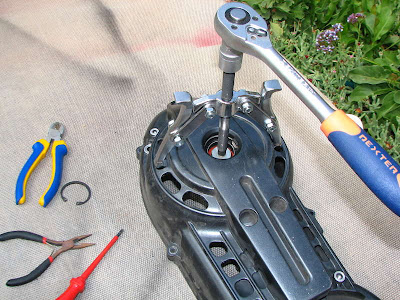
The extractor came in very handy here.

Old left, new right.

Mounting the new ball bearing is a bit complicated. Better try with the old one first.
You need to pat it with a hammer around the rim because it likes to settle in an angle and then lock up. So tap it with a hammer on the rim until it is straight and then you can use the extractor and press it in.
Sadly the ball bearing were not where my vibrations came from.
Wow sir you are still the best site ever, I also have a bit of a grinding noise and a harmonic vibration at 80 to 100 km hr, I have no Idea where to start, any suggestions? Rene, London,Ont, canada.
ReplyDeletewhen do you have the grinding noise? Some vibrations are normal, they sometime change / disappear when new rollers come in.
ReplyDeletegrinding noise seems to be there all the time it sounds that it comes from the crankshaft side(variator, the harmonic vibrations are a low hmmmm to high humm, MMMMMMmmmmmmMMMMMMmmmmmmm, at 83 km to 100 km and than settle down, replaced my rollers and belt no diffrence.
ReplyDeletegrinding noise can be a failing starter clutch, do you have any metal flakes in the oil? As to the harmonic vibration, I had it at different speeds, nothing to worry after over 40.000 km with them.
ReplyDeletehello,
ReplyDeletecan you give me the dimensions of the washer that goed betweet the front variator discs?
i allso need some more rpm when taking off, to get rid of the vibrations from too low rpm of the engine.
thanks! :-) Hannes.
Hi I have a Piaggio X10 executive 2013 with vibration what is wrong and how do I fix it?
ReplyDelete